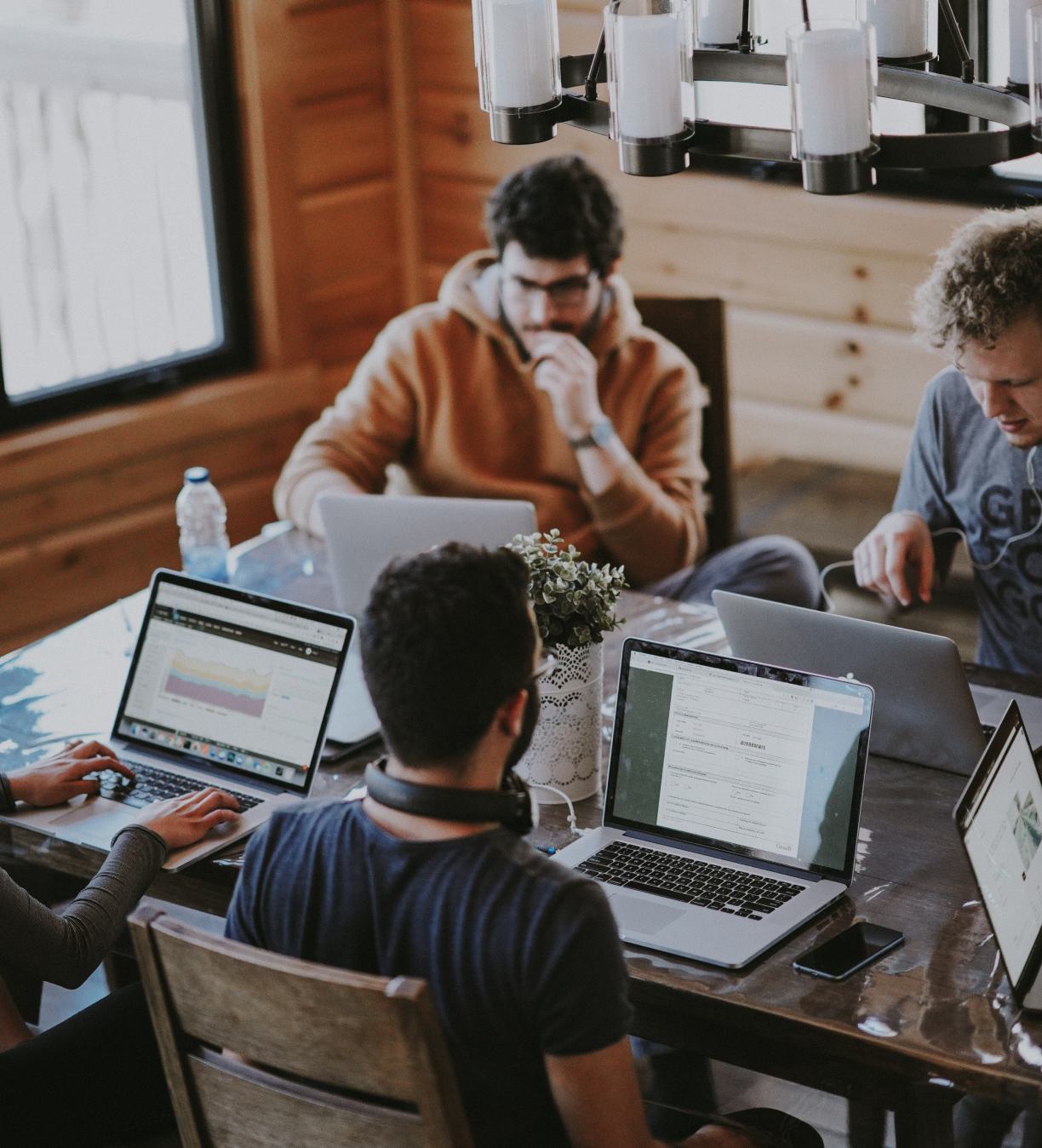
The Last Planner System: A Comprehensive Guide for Construction Professionals
The construction industry has long struggled with inefficiencies, delays, and cost overruns. Traditional project management methods, while effective to some degree, often fall short in addressing these challenges. The Last Planner System (LPS) is an innovative and collaborative approach that aims to tackle these issues head-on. Developed as part of the Lean Construction philosophy, LPS has gained widespread adoption among construction professionals who seek to improve project delivery, enhance communication, and reduce waste.
In this guide, we will explore what the Last Planner System is, how it works, and why it is a game-changer for construction projects. By the end of this article, you will have a solid understanding of LPS and how to implement it on your projects.
What is the Last Planner System?
The Last Planner System is a production planning and control system designed to improve the predictability and reliability of project workflows. It shifts the focus from traditional top-down planning to a more collaborative, bottom-up approach, where those closest to the work (the "last planners") are actively involved in the planning process. The system emphasizes the importance of making reliable commitments and ensuring that work is ready to be performed before it is scheduled.
LPS is built on the principles of Lean Construction, which aims to minimize waste and maximize value by optimizing the flow of work. It consists of several interconnected components that work together to create a smooth and predictable project flow.
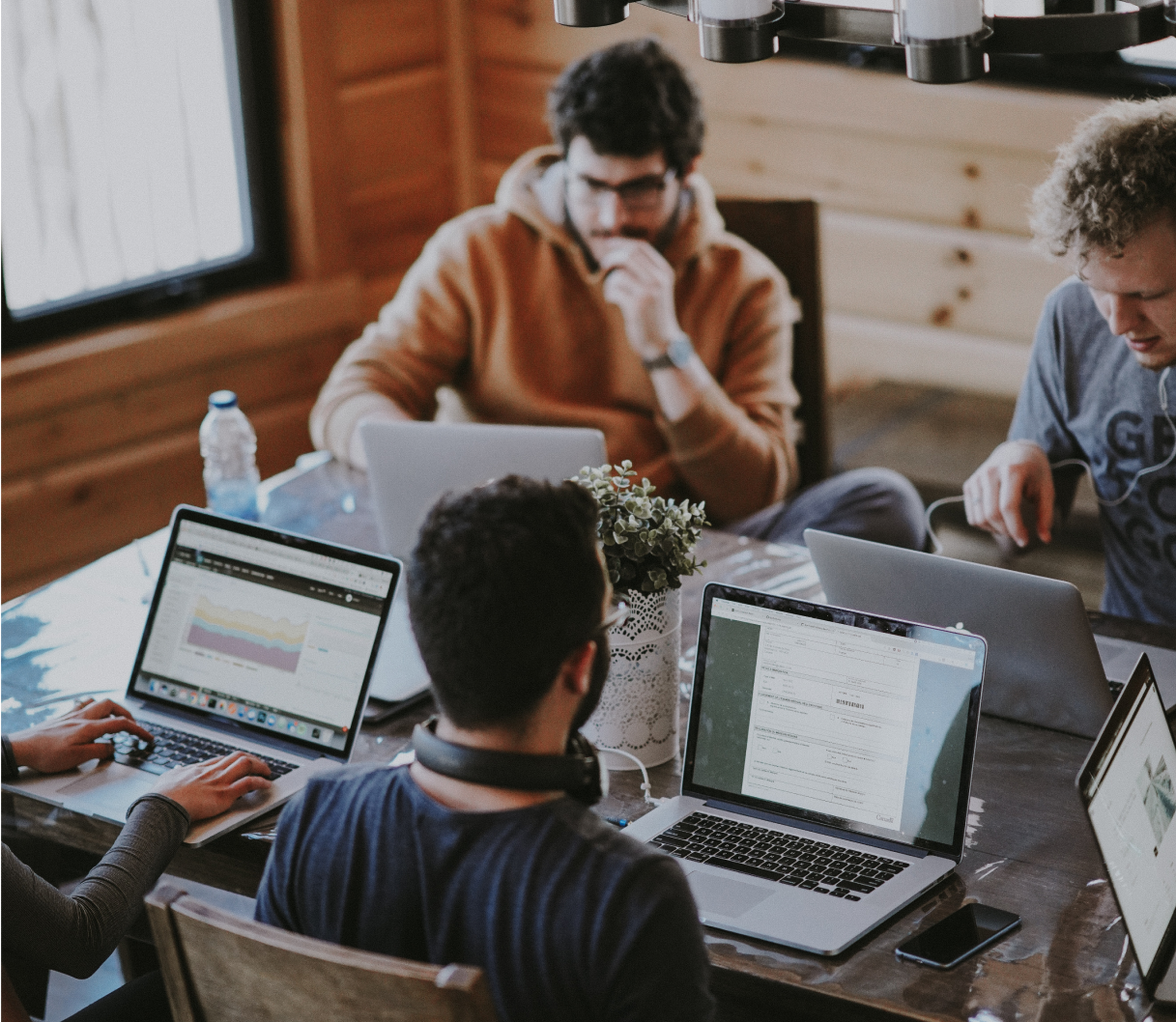
Key Components of the Last Planner System
Master Planning
The first component of LPS is Master Planning, where high-level milestones and project phases are established. This long-term plan provides a roadmap for the project, setting the overall direction and defining key objectives. However, unlike traditional planning methods, the Master Plan is not set in stone. It is a living document that can be adjusted as the project progresses and new information becomes available.
Phase Planning
Phase Planning, also known as Pull Planning, is the next level of detail in LPS. In this stage, the project team collaboratively works backward from key milestones to develop a detailed plan for each phase of the project. The goal is to create a sequence of activities that flows smoothly and efficiently, with each task being "pulled" into the schedule based on its readiness and the availability of resources. This collaborative approach ensures that all team members are aligned and that the plan is realistic and achievable.
Lookahead Planning
Lookahead Planning is a short-term planning process that focuses on the upcoming weeks or months. During this phase, the team identifies potential constraints and roadblocks that could hinder the progress of scheduled tasks. The goal is to make work ready by removing these constraints before the tasks are scheduled to begin. Lookahead Planning helps to ensure that the work scheduled for the near future is feasible and that the necessary resources, materials, and information are available.
Weekly Work Planning
Weekly Work Planning is where the rubber meets the road. In this stage, the last planners, who are typically foremen, superintendents, or other field supervisors, make commitments for the work that will be completed in the coming week. These commitments are based on the lookahead plan and the actual conditions on the ground. The key here is to make reliable promises—only committing to work that can be completed as planned. This builds trust and accountability among team members and helps to create a predictable workflow.
Daily Stand-Up Meetings
Daily Stand-Up Meetings are brief, focused meetings where the project team reviews the progress of the current day's work, identifies any issues or deviations from the plan, and makes adjustments as needed. These meetings are an essential part of LPS, as they allow for real-time communication and problem-solving. By addressing issues promptly, the team can prevent small problems from escalating into major delays.
Percent Plan Complete (PPC) Tracking
Percent Plan Complete (PPC) is a key performance metric used in LPS to measure the reliability of the planning process. It represents the percentage of tasks that were completed as planned in a given week. A high PPC indicates that the planning process is effective and that commitments are being met. If the PPC is low, it signals that there are issues in the planning process that need to be addressed. Tracking PPC helps the team to continuously improve and refine their planning practices.
Benefits of the Last Planner System
The Last Planner System offers numerous benefits for construction projects, including:
Improved Collaboration
LPS fosters a collaborative environment where all team members have a voice in the planning process. This leads to better communication, alignment, and understanding among the project team.
Increased Predictability
By involving those closest to the work in the planning process and focusing on making reliable commitments, LPS improves the predictability of project schedules and outcomes.
Reduced Waste
LPS helps to identify and eliminate waste by ensuring that tasks are only scheduled when they are ready to be performed. This reduces the likelihood of rework, delays, and resource inefficiencies.
Enhanced Accountability
The focus on making reliable commitments and tracking PPC creates a culture of accountability. Team members are more likely to follow through on their commitments when they know their performance is being measured.
Continuous Improvement
LPS encourages continuous improvement by regularly reviewing performance metrics and adjusting the plan as needed. This iterative approach helps to identify and address issues before they become major problems.
How to Implement the Last Planner System
Implementing the Last Planner System requires a cultural shift within the project team. It involves moving away from traditional top-down planning and embracing a more collaborative, bottom-up approach. Here are some steps to get started:
Educate the Team
Begin by educating the project team about the principles of Lean Construction and the Last Planner System. Provide training and resources to help them understand the benefits and processes involved.
Start Small
Consider implementing LPS on a pilot project or a specific phase of a larger project. This allows the team to become familiar with the system and work out any challenges before rolling it out on a larger scale.
Engage the Last Planners
Involve the last planners—those closest to the work—in the planning process from the outset. Their input is critical to creating a realistic and achievable plan.
Regularly Review and Adjust
Continuously monitor performance metrics such as PPC and hold regular meetings to review progress and make adjustments as needed. Encourage a culture of continuous improvement and learning.
Leverage Technology
Consider using project production management software such as P2IC which supports the Last Planner System. Digital tools can help streamline the planning process, improve communication, and track performance in real-time.
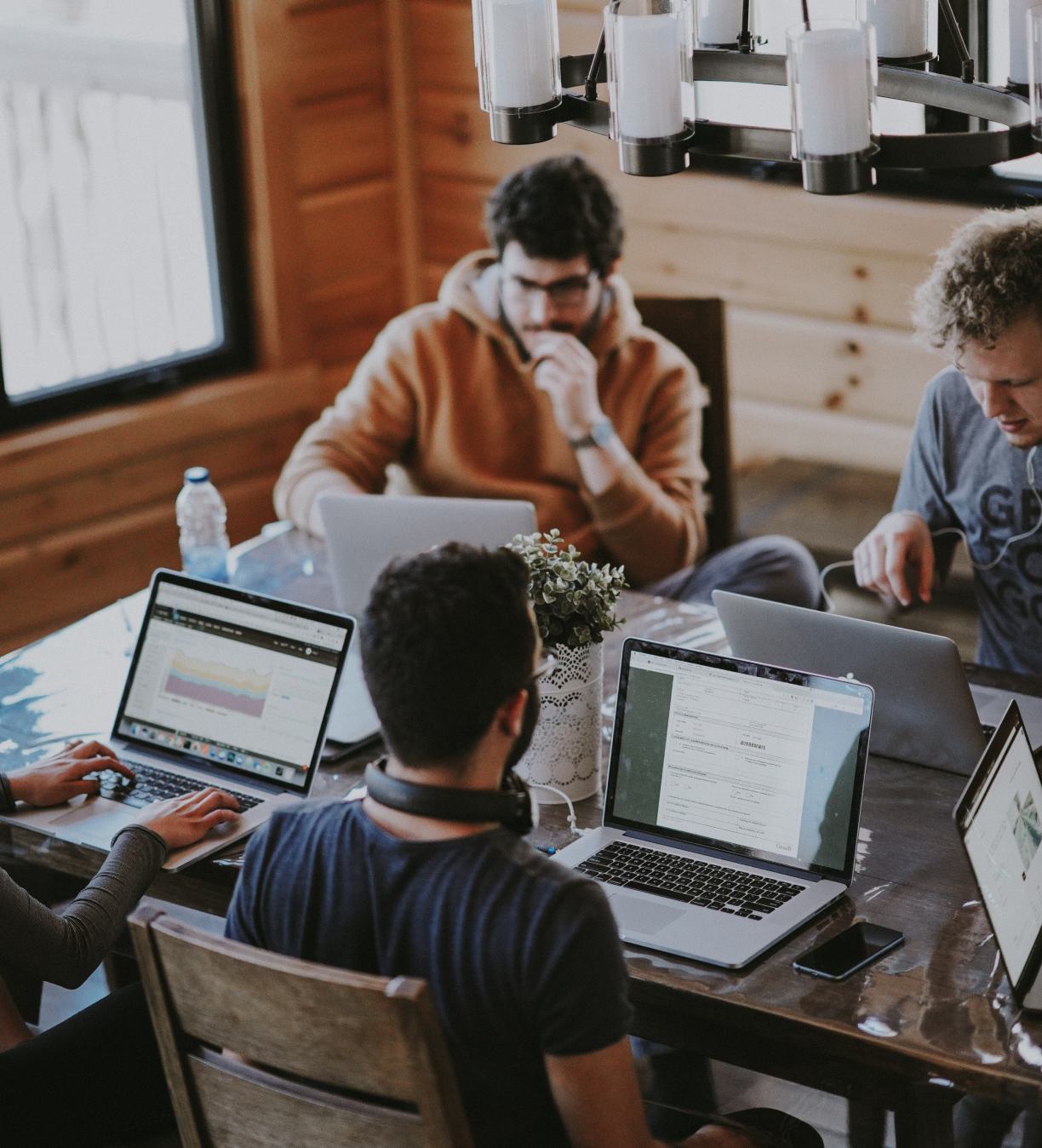
Conclusion
The Last Planner System is a powerful tool that can transform the way construction projects are planned and executed. By shifting the focus to collaboration, reliability, and continuous improvement, LPS helps to create a more predictable, efficient, and successful project delivery process. For construction professionals looking to improve project outcomes, the Last Planner System offers a proven approach that delivers tangible results.