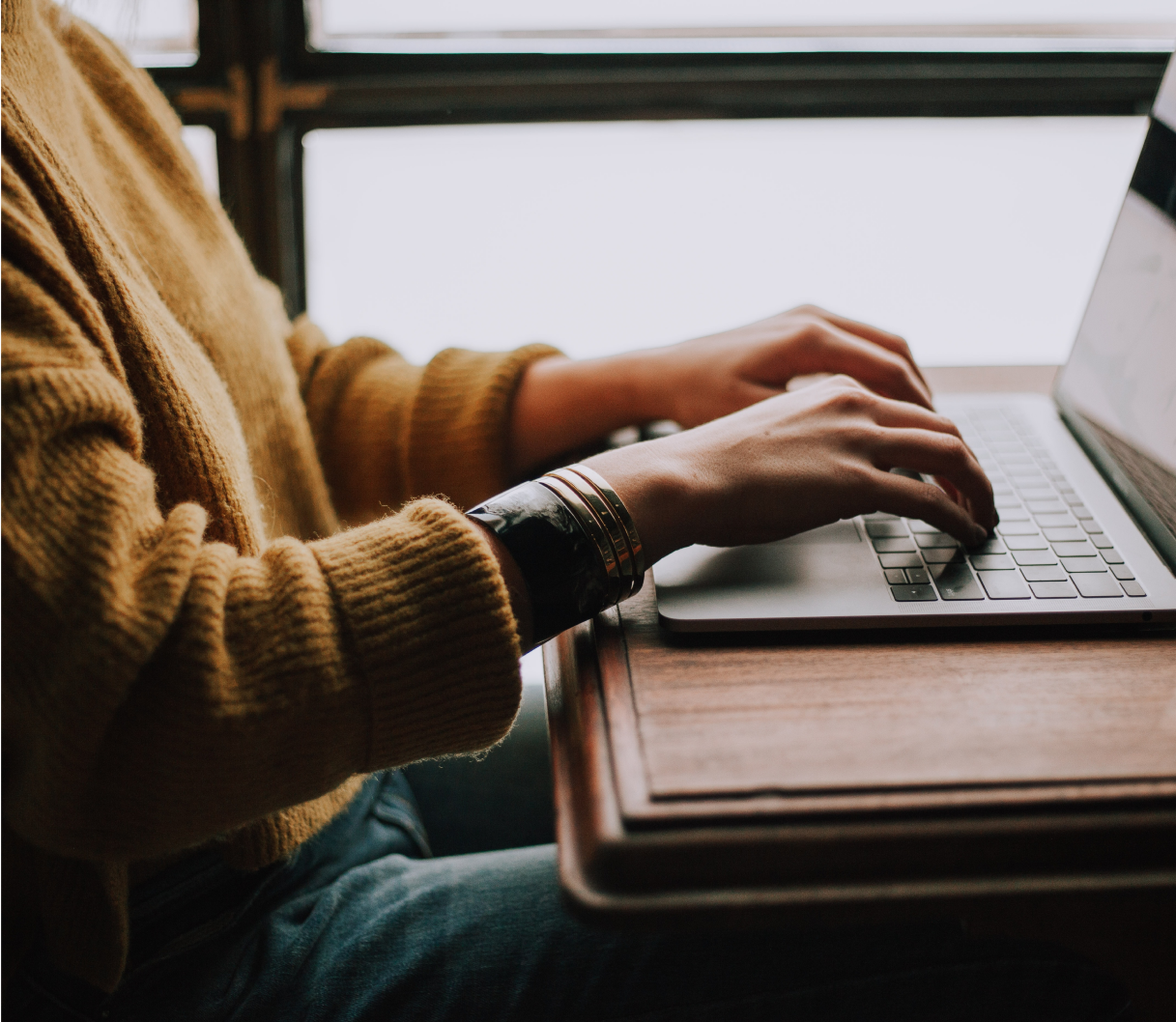
Lean Project Delivery: Transforming Construction for Predictable and Reliable Outcomes
In an industry historically plagued by inefficiencies, delays, and budget overruns, Lean Project Delivery (LPD) offers a fresh perspective and proven strategies to achieve predictable, reliable, and efficient results. Rooted in Lean Construction principles, LPD shifts the focus from traditional command-and-control management to a system that maximizes value, minimizes waste, and fosters collaboration.
We’ll explore Lean Project Delivery, its core principles, and how tools like the Last Planner System® (LPS) play a pivotal role in ensuring project success. Whether you’re a construction professional, project owner, or contractor, understanding LPD will position you to lead with authority and deliver exceptional results.
What Is Lean Project Delivery?
Lean Project Delivery is a structured framework designed to manage construction projects efficiently. It integrates design, construction, and operational phases, focusing on value creation and continuous improvement. Unlike traditional delivery methods, where cost and time overruns are common, LPD ensures that workflows are predictable, coordinated, and aligned with client needs.
At its heart, LPD embodies the philosophy of Lean Construction, which aims to:
Eliminate Waste: Avoiding unnecessary tasks, delays, and rework.
Maximize Value: Prioritizing what the client truly needs.
Enhance Collaboration: Encouraging transparency and teamwork among all stakeholders.
The Principles of Lean Project Delivery
LPD is guided by five key principles that serve as the foundation for every project phase:
1. Collaborative Planning
Effective planning requires active participation from all stakeholders—owners, designers, contractors, and suppliers. Collaboration ensures that everyone is aligned on goals, constraints, and workflows.
This collaborative approach fosters:
Early Problem Identification: Resolving potential issues before they escalate.
Shared Accountability: Ensuring everyone takes responsibility for project outcomes.
2. Pull Scheduling
Traditional construction schedules often push tasks forward based on assumptions, leading to inefficiencies. Pull scheduling flips this model, focusing on downstream requirements to drive upstream activities.
For example, rather than beginning construction based solely on deadlines, pull scheduling considers when materials, approvals, and resources will realistically be ready. This minimizes delays and ensures that work progresses smoothly.
3. Waste Reduction
In Lean terms, "waste" refers to anything that doesn’t add value to the project. Common examples in construction include waiting, overproduction, rework, and unnecessary movement. LPD aims to:
Identify sources of waste.
Continuously refine processes to eliminate inefficiencies.
4. Reliability of Commitments
LPD emphasizes the importance of reliable promises. Teams must only commit to tasks they can realistically complete. This reduces frustration and improves trust between project participants.
5. Continuous Improvement (Kaizen)
Construction projects are dynamic, with challenges emerging at every stage. LPD encourages teams to regularly review performance, learn from mistakes, and implement improvements.
The Role of the Last Planner System® in Lean Project Delivery
The Last Planner System® (LPS) is the backbone of Lean Project Delivery. Developed by Glenn Ballard and Greg Howell, LPS is a collaborative planning tool designed to improve workflow reliability and enhance project performance.
How LPS Works:
Master Planning:
High-level planning that identifies major milestones and sets the overall project direction.
Phase Planning:
Breaking the project into phases, with a focus on aligning work sequences and dependencies.
Lookahead Planning:
A six- to eight-week window where constraints are identified and removed. This step ensures that upcoming tasks are executable.
Weekly Work Planning:
Short-term plans where teams commit to specific tasks, ensuring alignment with the broader schedule.
Plan Percent Complete (PPC):
A metric that tracks how many planned tasks were completed on time, helping teams improve planning reliability over time.
The strength of LPS lies in its ability to connect long-term plans with day-to-day execution. By focusing on collaboration, realism, and accountability, it reduces the chaos and unpredictability often associated with construction projects.
Benefits of Lean Project Delivery
Adopting Lean Project Delivery offers numerous benefits for all stakeholders, including project owners, contractors, and designers.
1. Improved Predictability
LPD ensures that workflows are well-coordinated, reducing delays and improving the likelihood of meeting project deadlines and budgets.
2. Increased Productivity
By eliminating waste and focusing on efficient workflows, LPD enables teams to achieve more with less effort and fewer resources.
3. Enhanced Collaboration
The emphasis on shared accountability and open communication fosters trust and transparency among all project participants.
4. Higher Quality Outcomes
LPD’s focus on continuous improvement and reliability leads to fewer errors, defects, and rework, resulting in higher-quality deliverables.
5. Greater Client Satisfaction
By prioritizing value creation and delivering predictable outcomes, LPD enhances client confidence and satisfaction.
Challenges in Implementing Lean Project Delivery
While the benefits are compelling, implementing LPD is not without challenges:
1. Cultural Resistance
Construction teams accustomed to traditional methods may resist the collaborative and iterative nature of LPD.
Solution: Provide training and education to demonstrate the advantages of Lean principles.
2. Coordination Across Teams
LPD requires seamless communication and collaboration, which can be challenging in fragmented supply chains.
Solution: Use digital tools like Building Information Modeling (BIM) to enhance coordination.
3. Commitment to Change
LPD is a long-term investment that requires continuous effort. Teams must be willing to embrace the principles fully to see results.
Solution: Start small, implementing Lean principles on pilot projects before scaling up.
Practical Steps to Adopt Lean Project Delivery
Start with Education: Ensure all team members understand the principles of Lean Construction and the Last Planner System®.
Build a Collaborative Culture: Encourage open communication and shared accountability across all project participants.
Leverage Technology: Utilize digital tools to enhance planning, coordination, and visibility.
Track and Measure Progress: Use metrics like PPC to monitor performance and identify areas for improvement.
Commit to Continuous Improvement: Regularly review processes, learn from challenges, and refine workflows.
Positioning Yourself as a Leader in Lean Project Delivery
Adopting Lean Project Delivery not only transforms how you manage construction projects but also positions you as a thought leader in the industry. By championing these principles, you can:
Build Trust with Clients: Demonstrate your commitment to delivering predictable, high-quality outcomes.
Enhance Your Reputation: Become known for innovation, efficiency, and reliability.
Drive Industry Change: Inspire others to adopt Lean practices, contributing to a more efficient and sustainable construction sector.
Conclusion
Track work across the enterprise through an open, collaborative platform. Link issues across Jira and ingest data from other software development tools, so your IT support and operations teams have richer contextual information to rapidly respond to requests, incidents, and changes.